Polymer design
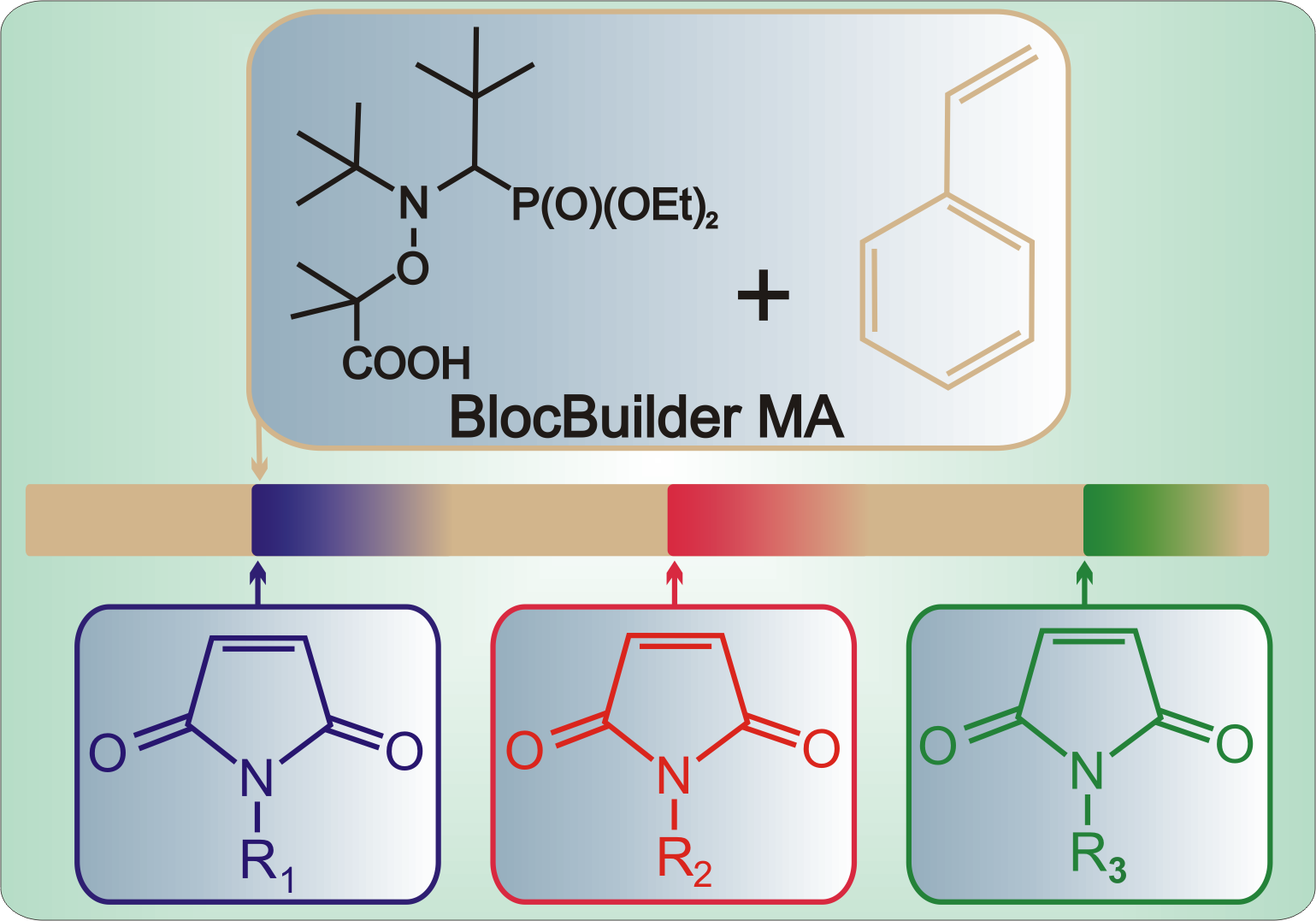
Polymeric materials - allowing to realise both commodity and high-tech applications – are widely used in many important industrial sectors, such as construction, information technology and health care, as well as in the pharmaceutical and chemical industry. Designing polymer production processes is not only needed to expand these industries’ application ranges but also to avoid the formation of off-spec material and to make sure that energy resources are optimally used.
This research theme specifically aims at the design of new polymeric materials up to industrial scale, considering advanced multi-scale computational tools. Our goal is to take control over the entire microstructure of individual polymer chains, taking into account economic and environmental constraints. Important aspects covered are a fundamental understanding of the (de)polymerisation kinetics, sustainable scale-up of polymerisation processes, and the detailed characterisation of polymer products so that structure-property relations can be identified.
Our key research questions:
- How can a complete characterisation of the polymer product be obtained to enable process control?
- How can the complex interplay between chemical and diffusion phenomena be regulated to facilitate the production of high-tech polymeric materials?
- How can a transition be made to water-based polymerization processes?
- What are the most relevant industrial polymer production protocols, accounting for safety regulations?
The following topics are part of the Polymer design research theme:
Customizing the design of complex macromolecular architectures
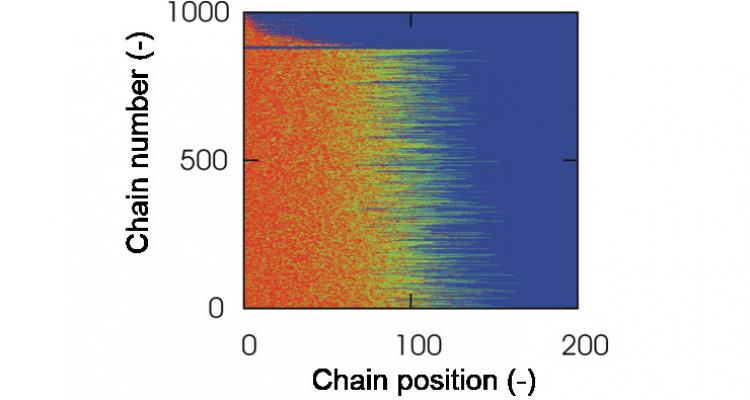
For advanced polymeric applications, such as drug delivery systems and coatings, each individual macromolecule needs to be customized with respect to its monomer sequences and location of branches. Using advanced computer algorithms, a full characterization - and thus design - of these individual macromolecules is possible.
Design and optimization of industrial dispersed phase polymerization reactors
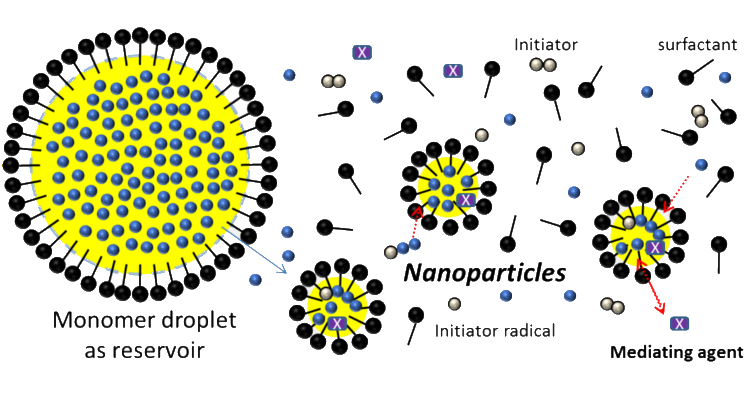
The regulated grow of the particle size distribution up to high solid contents is a major industrial challenge for the design of dispersed phase polymerization processes in aqueous media. Advanced algorithms - implemented in user friendly computer codes – allow the design and optimization of industrial dispersed phase polymerization reactors.
Scaling up reactors for radical polymerization in a safe and effective way
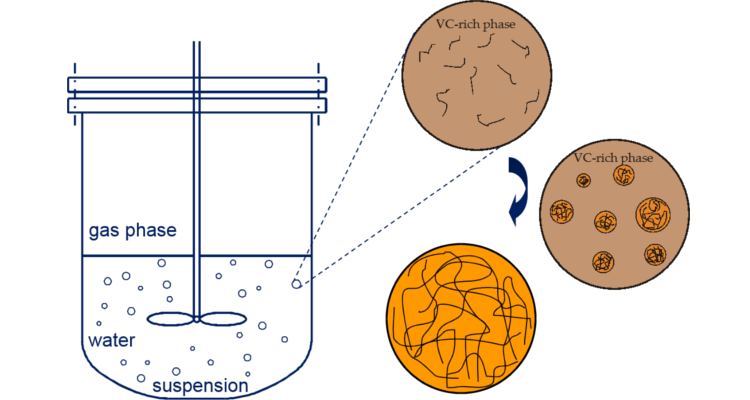
Radical polymerization processes are characterized by a high exothermicity, particularly when using large reactors. This may not only lead to a considerable increase of temperature, but also to strongly deviating temperatures within the different zones of the reactor. As a result, safety is compromised and the product will be influenced by inhomogeneities and runaway. LCT developed commercial software to take care of these problems.
Designing numerical methods for chain-growth processes
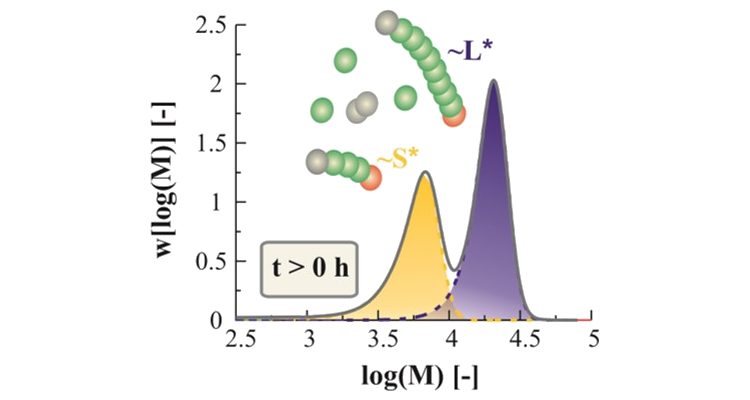
Several chemical processes include a chain or step-growth mechanism, in which species with different chain lengths are created. Deterministic as well as stochastic methods are developed in order to describe and design these chemical process into detail, including depolymerization.
Developing environmentally benign processes for kinetics in liquid phase
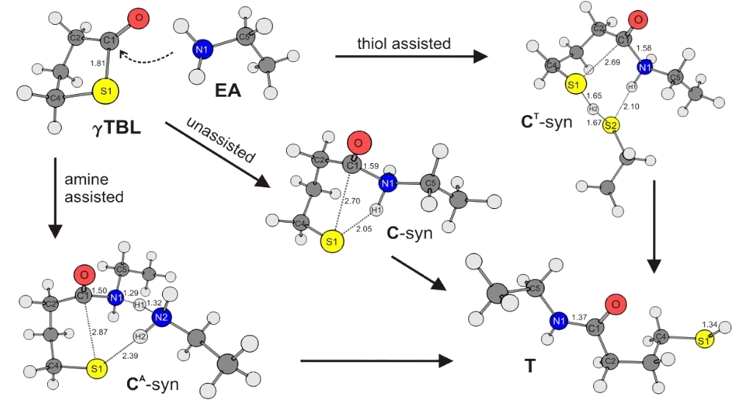
Fundamental understanding of reaction mechanisms in liquid phase - such as environmentally benign processes in the aqueous phase - requires accurate intrinsic rate coefficients. To this end, both dedicated experiments and liquid-phase computational chemistry can be applied.
Developing efficient polymer materials and processing units
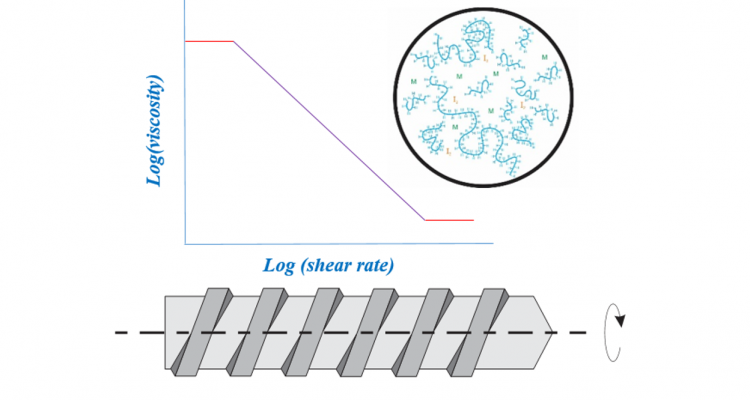
The production of polymeric materials needs to be efficient in view of economic and environmental constraints. Multi-scale modeling tools are developed to ensure a desired polymer flow. LCT software accounts for the interplay of pressure variations and reactivity changes, including surface modifications.
Closing the loop for polymer engineering applications and waste
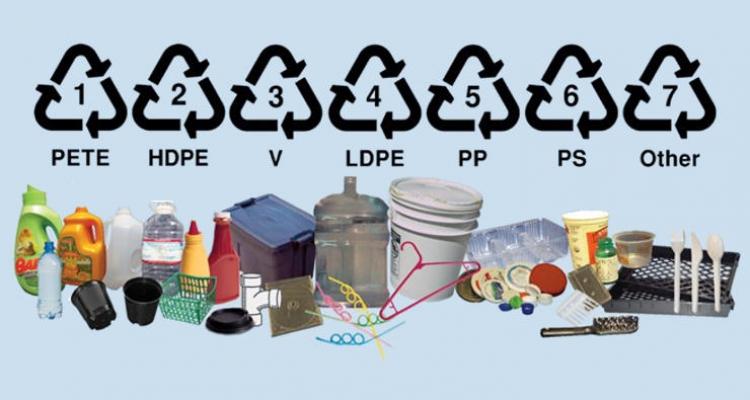
An important societal challenge is the development of novel chemical routes and technologies to enable polymer recycling. Model-based design is combined with experimental validation to be successful in this respect.
Lifting data analysis and storage to chemical processes
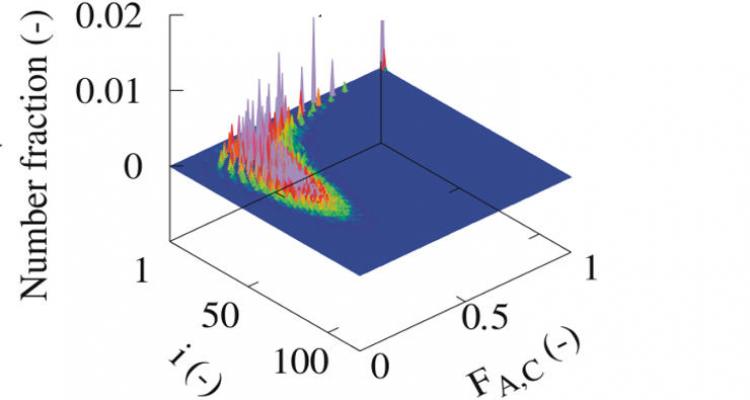
Chemical processes are influenced by billions of simultaneous phenomena. Here we developed and apply smart algorithms to provide process design from molecule to plant level.
Multi-functional nanostructured materials
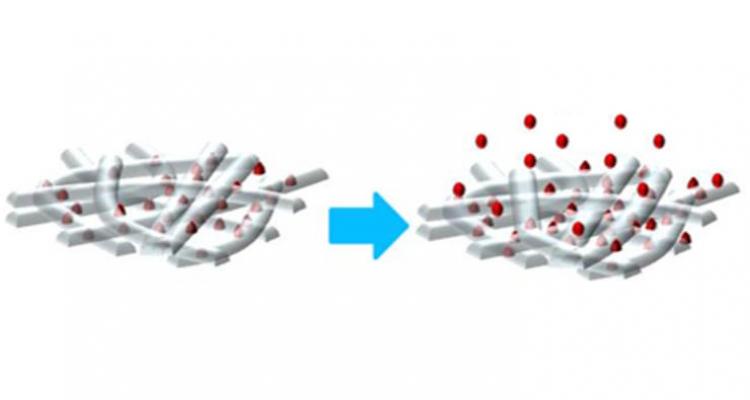
Next-generation material production aims at combining several functionalities to enable property flexibility. In combination with nanoscience unprecedented application potential can be achieved.
Process intensification for carbon neutral chemical industry
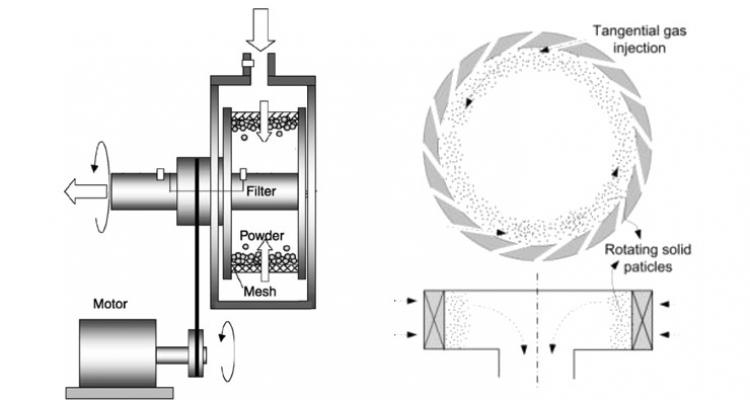
Reducing the footprint of chemical reactors by ensuring higher heat, mass and/or momentum transfer is desirable for a wide range of commercial and emerging processes, such as drying, fast gas–solid reactions and steam cracking. These processes are being studied in unique modular setups with on-line product analysis.