Reactor engineering

Optimal use of resources asks for the design of the ‘ideal’ reactor where less valuable products are converted into more valuable ones with the highest possible selectivity. As such the cost for the overall process will be significantly reduced. Improved sustainability, environmental performance, and efficiency via e.g. the development of innovative equipment are important targets, requiring that process intensification is a constant point of attention in chemical engineering research.
This research theme aims at the full exploitation of existing reactor technologies and the development of new reactor technologies. Main focus is on the study of the delicate interplay between reaction kinetics and mass, energy and momentum exchange phenomena. Given the large scale of most commercial chemical processes, the smallest improvement in reactor design has a huge impact on the use of resources and the operating costs.
Our key research questions:
- Which shifts in reactor operating conditions will improve the reactor performance?
- What are the consequences of the smallest shift in reactor technology on the interplay between chemistry and hydrodynamics?
- How to develop and validate numerical models to study reactor improvement and design, given costly and time-consuming experimental research?
The following topics are part of the Reactor engineering research theme:
Verifying the behavior of hydrodynamics in vortex units
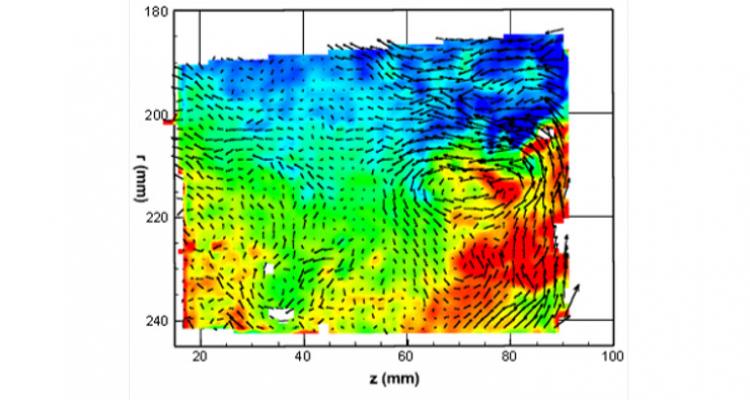
The effect of operating variables on gas-solid phase hydrodynamics is investigated both experimentally and numerically. Pressure probes and Stereo Particle Image Velocimetry measurements provide experimental data, allowing to verify hydrodynamic models for both single and multi-phase flow.
Investigating heat and mass transfer in vortex units

The effect of unit geometry and operational variables on the hydrodynamic performance - as well as on the reactor and powder scale heat and mass transfer -, is investigated in an adiabatic scaled-down gas-solid vortex unit. Correlations for the dimensionless groups describing the transfer rate dependencies on geometry and process conditions are developed.
Scale-up and advanced experimentation for sustainability improvement
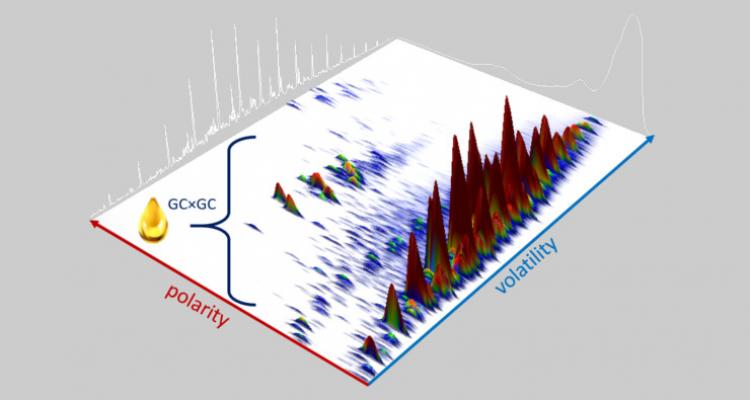
Minimizing energy consumption, evaluating renewable feedstocks, novel refractory and the use of certain reactor materials all contribute to make the chemical industry more sustainable. Advanced experimentation on lab and pilot scale allows to assess all these phenomena and gain fundamental understanding relevant for the process level.
Computational Fluid Dynamics of reactive flows
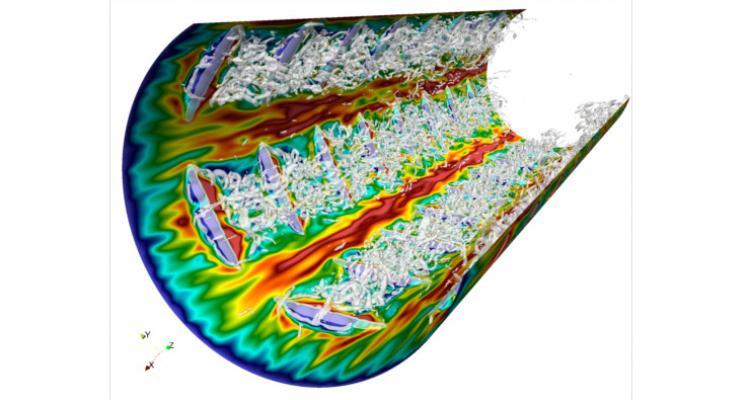
The use of traditional reactor models, such as a perfectly mixed or plug flow model, are insufficient when temperature and concentration gradients become important. In order to account for interactions between transport and reaction phenomena, Computational Fluid Dynamics (CFD) are applied. Transport of mass, energy and momentum are described using in-house developed as well as and commercial CFD codes.
Process modelling and techno-economic analysis
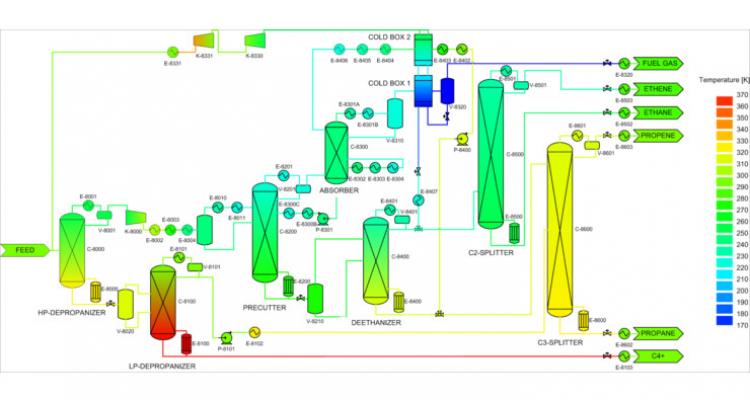
User friendly computer codes – such as Aspen Plus process simulation software - allow for a fast and thorough analysis of chemical processes for a wide range of operating conditions, reactor configurations and feedstock compositions. The software calculates both capital expenditure (CAPEX) and operational expenditure (OPEX) and also incorporates recycling applications and exergie levels.
Deploying LCT’s MicroKinetic Engine to make kinetics accessible
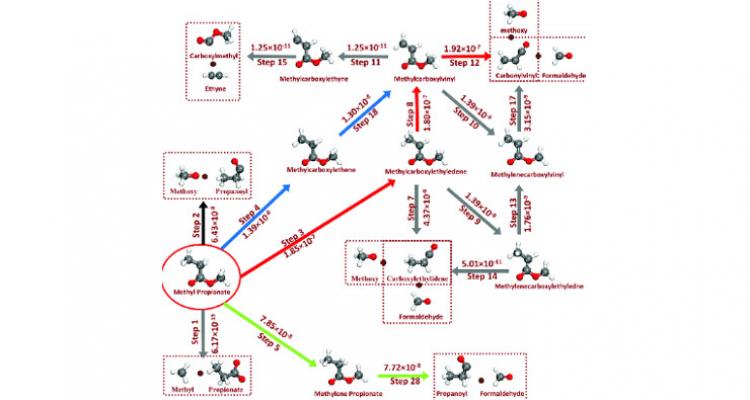
Microkinetic model development strives to integrate all independently acquired experimental and theoretical information about the investigated reaction. LCT’s MicroKinetic Engine (μKE) allows to unravel complex chemical reactions with a few mouse clicks. Kinetic performance can be simulated for different reactor types and compared with experimental data. The software provides direct feedback on model adequacy and predictability through data visualization and statistical interpretation.
Design and optimization of industrial dispersed phase polymerization reactors
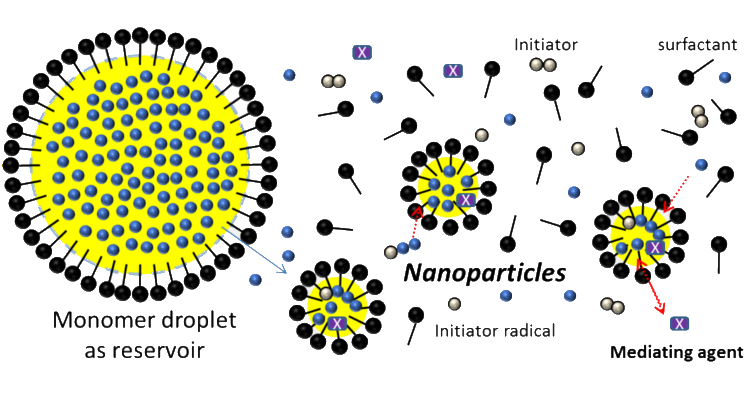
The regulated grow of the particle size distribution up to high solid contents is a major industrial challenge for the design of dispersed phase polymerization processes in aqueous media. Advanced algorithms - implemented in user friendly computer codes – allow the design and optimization of industrial dispersed phase polymerization reactors.
Scaling up reactors for radical polymerization in a safe and effective way
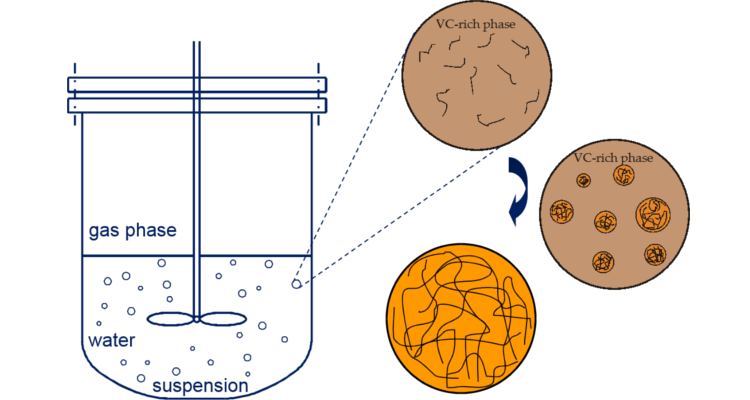
Radical polymerization processes are characterized by a high exothermicity, particularly when using large reactors. This may not only lead to a considerable increase of temperature, but also to strongly deviating temperatures within the different zones of the reactor. As a result, safety is compromised and the product will be influenced by inhomogeneities and runaway. LCT developed commercial software to take care of these problems.
Bringing Industry 4.0 to chemical processes
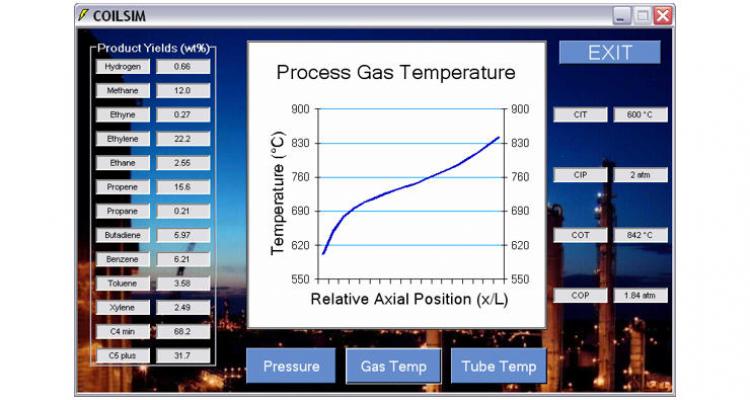
Integration of smart production and advanced information technology is covered to facilitate the transition to next-generation reaction synthesis and chemical production.