Circular process design

Our society needs to be smarter. Today we must consider the whole lifecycle of our resources. For example closing the cycle on plastics could reduce import dependency by 80% in terms of fossil fuels for plastics production. Together with steel, aluminum and cement, plastics have been identified as one of the most promising materials to reduce our carbon footprint in Europe. Fundamental changes are needed in all these parts of the process industry, in particular in the design of these processes where exergy analysis, resource efficiency and life cycle analysis are fed by fundamental process simulation data that account accurately for the important chemical and physical phenomena on different scales. This more circular, and smarter economy has tremendous potential for Europe and in particular Flanders because of its population density and existing logistics infrastructure.
Scale-up is thus based on the fundamental understanding of processes using first principles based process simulation and design, a key expertise within the Centre for Sustainable Chemistry (CSC: https://www.csc.ugent.be & Elisabeth Delbeke(external link)). The developed simulation models are generated automatically, use primarily ab-initio derived thermodynamic and kinetic data, are applied with in-house developed solvers (e.g. COILSIM1D: https://www.avgi.be), and can be even coupled with Fluent or OpenFOAM. Success stories are not limited to: chemical recycling of plastic waste, biomass fast pyrolysis, steam cracking for olefin production, gasification, catalytic cracking, polymer production, etc.
The new research challenges, both fundamentally and on the process side are:
- How do you scale-up a technology in a sustainable way?
- How can you transfer data from lab scale to industrial scale and what is the accuracy?
- How can product compositions be measured on-line for hetero atom containing mixtures?
- How do we develop simulation tools that give users accurate results within fractions of seconds?
- How can we characterize complex solid and liquid feedstocks and relate this with detailed models?
More fundamentally:
- How do you quantify uncertainty on model and experimental data?
- Can we implement detailed kinetic models in CFD simulations?
- Can we measure intrinsic kinetics of thermochemical process starting from solids?
- How is turbulence reliably modeled?
- How can we make compact kinetic models automatically?
- Can we do on-the fly ab-initio calculations?
The following topics are part of the Circular process design research theme:
Scale-up and advanced experimentation for sustainability improvement
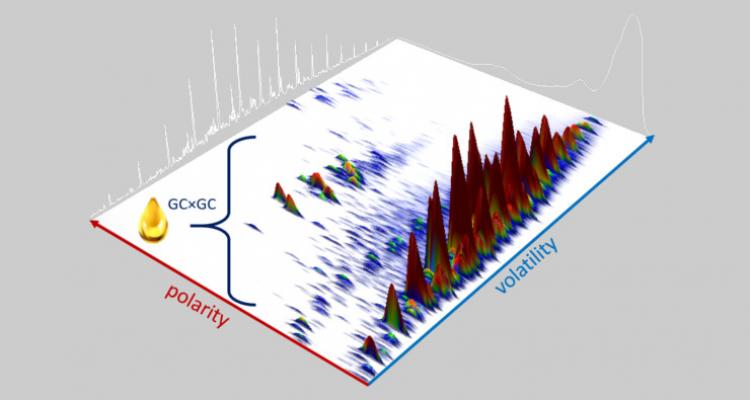
Minimizing energy consumption, evaluating renewable feedstocks, novel refractory and the use of certain reactor materials all contribute to make the chemical industry more sustainable. Advanced experimentation on lab and pilot scale allows to assess all these phenomena and gain fundamental understanding relevant for the process level.
Plastics chemical recycling and biomass valorization
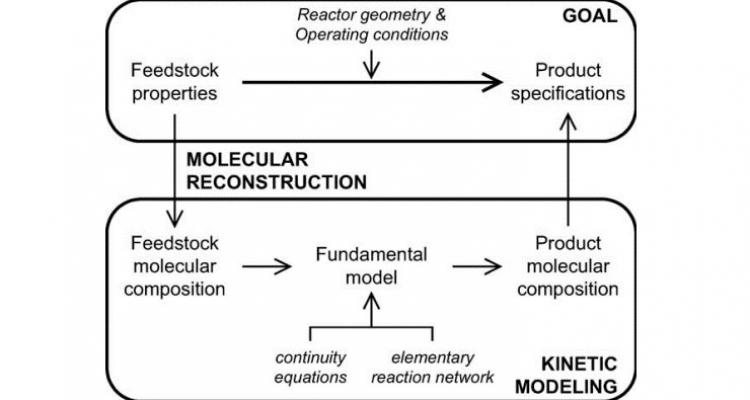
Using a unique infrastructure for detailed characterization - such as comprehensive two-dimensional gas chromatography (GC × GC) and comprehensive LC equipment -, allows to obtain valuable new information about waste and alternative feedstocks valorisation. In combination with feedstock reconstruction, process evaluations can be executed in silico with unprecedented accuracy.
Process intensification for carbon neutral chemical industry
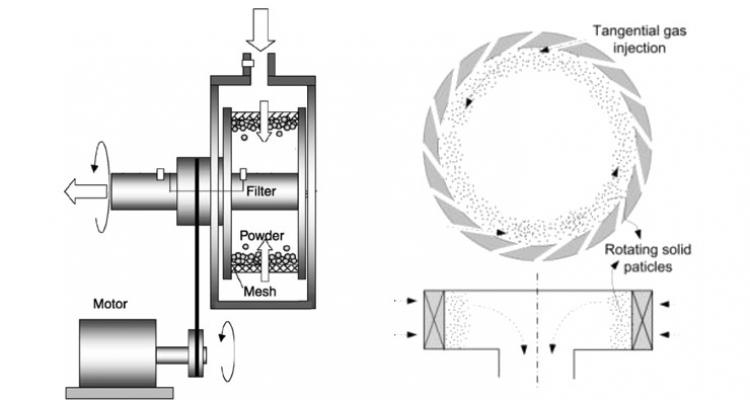
Reducing the footprint of chemical reactors by ensuring higher heat, mass and/or momentum transfer is desirable for a wide range of commercial and emerging processes, such as drying, fast gas–solid reactions and steam cracking. These processes are being studied in unique modular setups with on-line product analysis.
Process modelling and techno-economic analysis
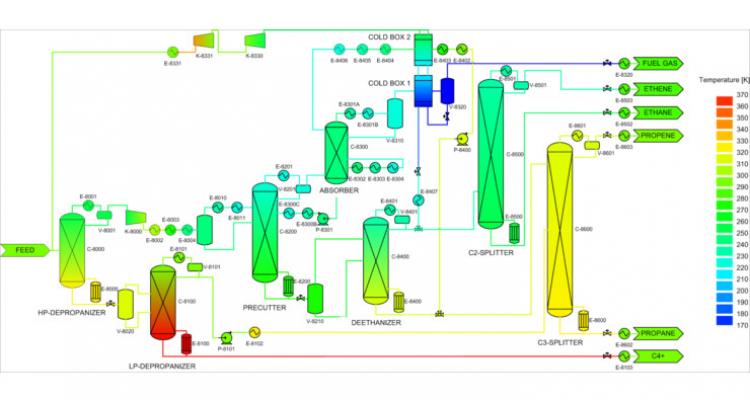
User friendly computer codes – such as Aspen Plus process simulation software - allow for a fast and thorough analysis of chemical processes for a wide range of operating conditions, reactor configurations and feedstock compositions. The software calculates both capital expenditure (CAPEX) and operational expenditure (OPEX) and also incorporates recycling applications and exergie levels.
Computational Fluid Dynamics of reactive flows
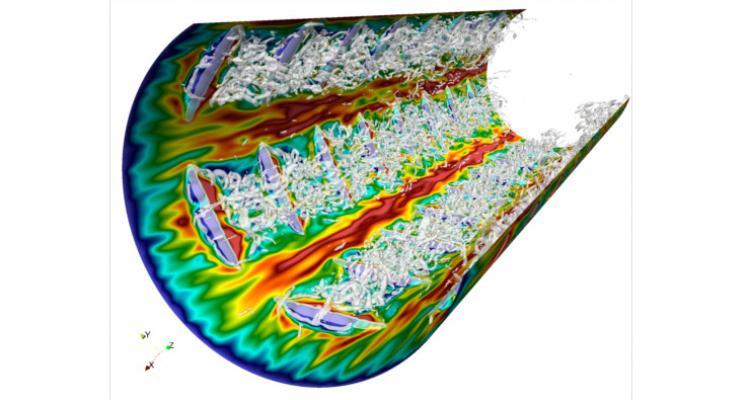
The use of traditional reactor models, such as a perfectly mixed or plug flow model, are insufficient when temperature and concentration gradients become important. In order to account for interactions between transport and reaction phenomena, Computational Fluid Dynamics (CFD) are applied. Transport of mass, energy and momentum are described using in-house developed as well as and commercial CFD codes.
Developing an automatic chemical reaction mechanism generator to optimize computer simulations
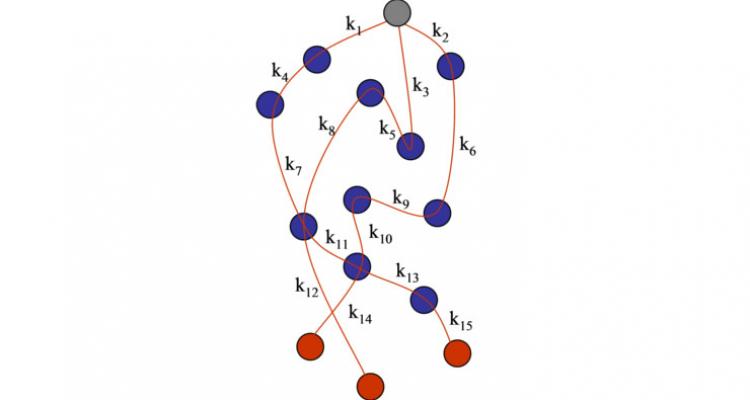
Developing or optimizing chemical reactors based on computer simulations is becoming indispensable in the chemical industry, as this allows to circumvent the use of expensive and time consuming experiments. The development of GENESYS, an automatic chemical reaction mechanism generator which is able to build kinetic models – composed of elementary chemical reaction steps -, is an important step to improve the value and applicability of computer simulations.
Verifying the behavior of hydrodynamics in vortex units
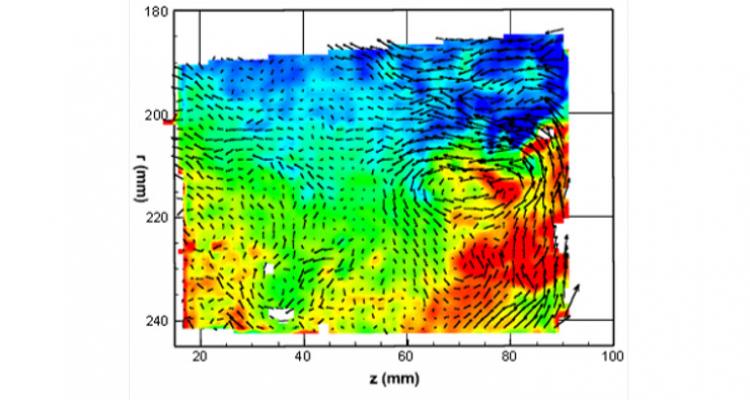
The effect of operating variables on gas-solid phase hydrodynamics is investigated both experimentally and numerically. Pressure probes and Stereo Particle Image Velocimetry measurements provide experimental data, allowing to verify hydrodynamic models for both single and multi-phase flow.
Operando and in-situ material characterization
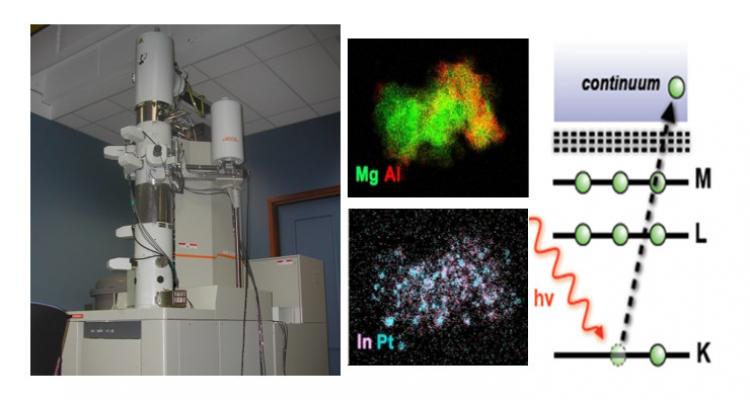
Characterization is an indispensable part of catalyst and material research. Phase, composition, elemental oxidation state, particle size and shape all join in determining the activity and stability of materials. In addition to information regarding the as-prepared and post-mortem state, an insider’s view into the material during operation is of great value. Hence the importance of operando characterization, allowing a direct connection between physico-chemical properties and performance.
Deploying LCT’s MicroKinetic Engine to make kinetics accessible
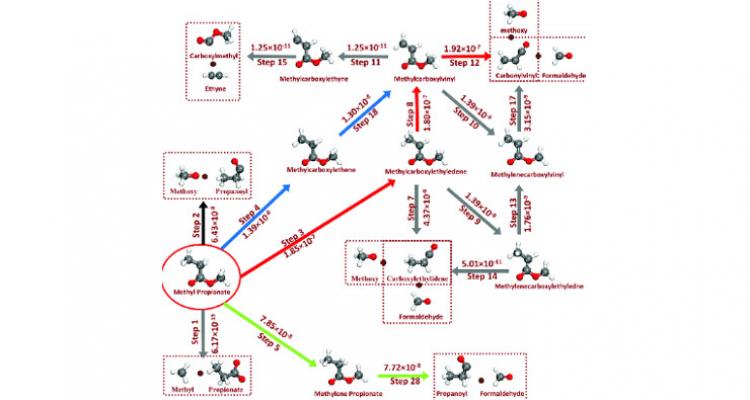
Microkinetic model development strives to integrate all independently acquired experimental and theoretical information about the investigated reaction. LCT’s MicroKinetic Engine (μKE) allows to unravel complex chemical reactions with a few mouse clicks. Kinetic performance can be simulated for different reactor types and compared with experimental data. The software provides direct feedback on model adequacy and predictability through data visualization and statistical interpretation.
Providing chemical insights to use biomass as a resource for high-value chemicals
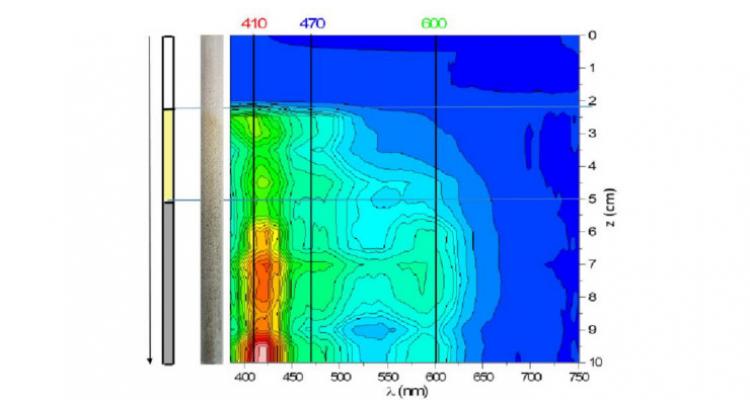
The diversity of functional groups makes biomass an interesting resource for chemicals. To be economical feasible, all biomass components need to be valorized. Experimental and theoretical studies provide the chemical insight needed to optimize the yields of high-value chemicals and upgrade lower-value products.
Designing kinetic models to optimize biomass conversion into green, next-generation fuels
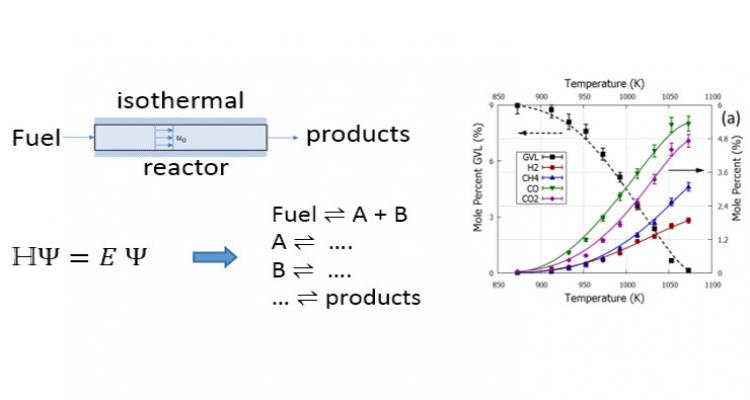
Thermal (catalytic) biomass conversion to green, next-generation fuels provides a promising means to reduce the carbon footprint and the emission of dangerous particulates. Experimental and theoretical studies lead to detailed kinetic models needed to optimize fuel production and to assess fuel performance.
Bringing Industry 4.0 to chemical processes
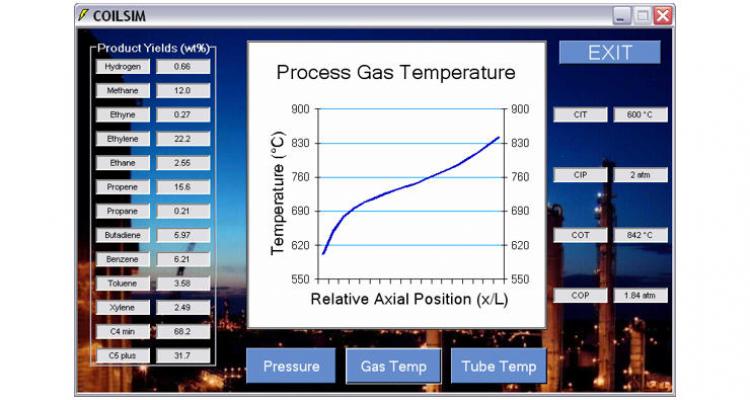
Integration of smart production and advanced information technology is covered to facilitate the transition to next-generation reaction synthesis and chemical production.
Closing the loop for polymer engineering applications and waste
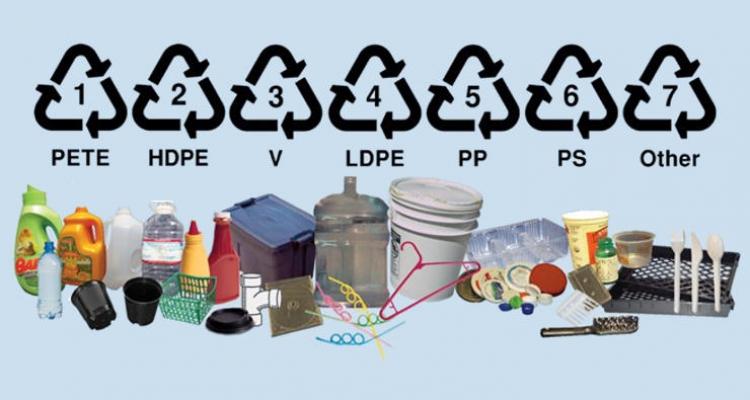
An important societal challenge is the development of novel chemical routes and technologies to enable polymer recycling. Model-based design is combined with experimental validation to be successful in this respect.
Creating efficient energy use and exergy analysis
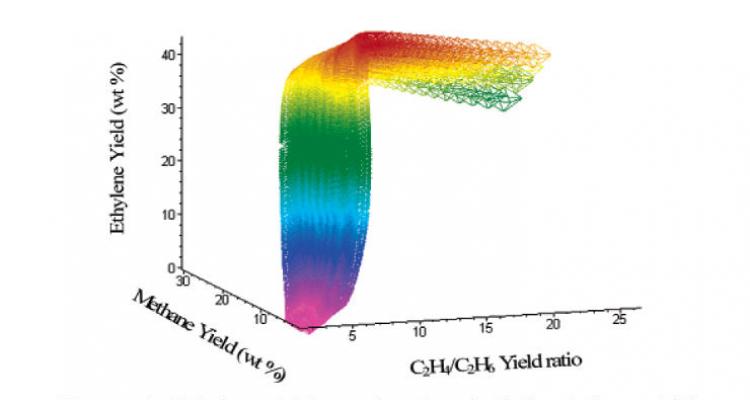
A key challenge for industrial production processes is their energy efficient operation. Here optimal conditions towards maximal performance are identified for thermal and catalytic processes including polymerization.
Chemical looping as a technology platform
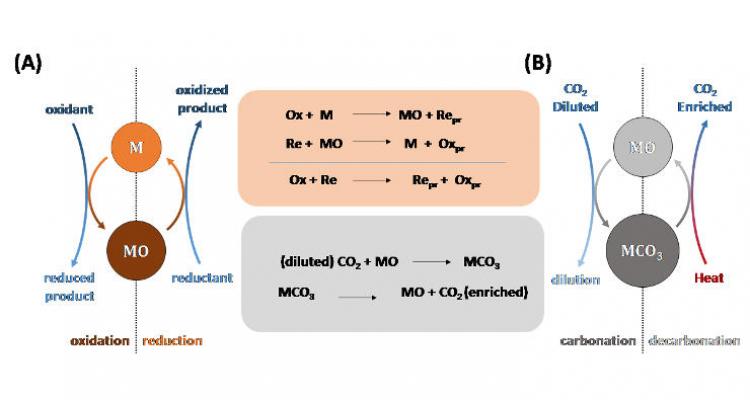
We aim to demonstrate that chemical looping has large potential, well beyond combustion, as a flexible technology platform for process intensification in fuel processing technology. The product separation that is inherent to this technology can have significant impact in the future on a broad range of chemical processes, with higher efficiency and ‘greener’ chemistry.
Lifting data analysis and storage to chemical processes
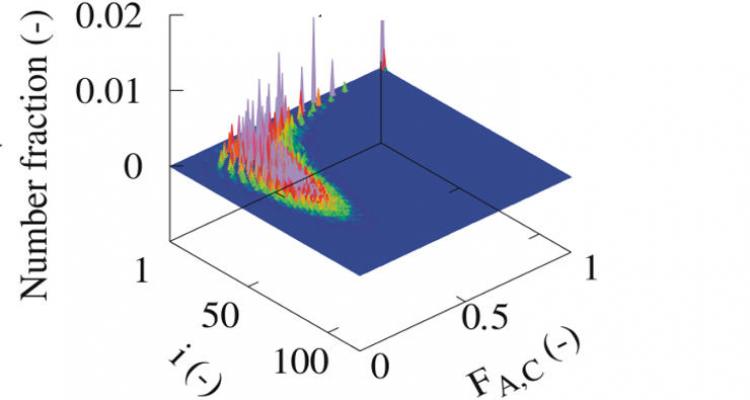
Chemical processes are influenced by billions of simultaneous phenomena. Here we developed and apply smart algorithms to provide process design from molecule to plant level.